Cost-Effective Assembly Solutions: The Advantage of Using Cobot Arms
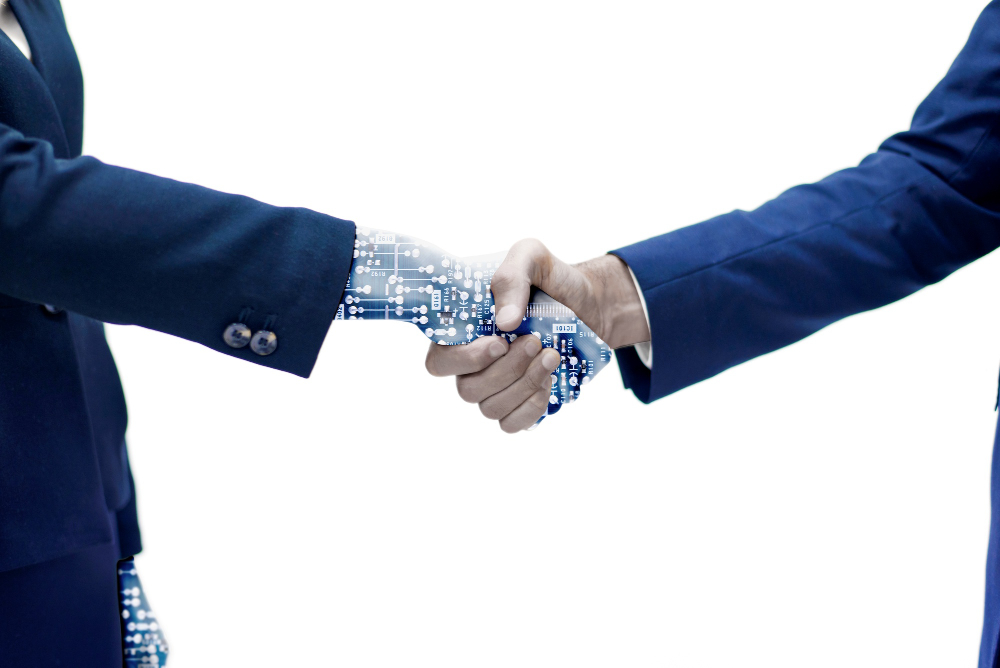
In today’s rapidly evolving manufacturing landscape, companies are constantly seeking ways to reduce costs, enhance efficiency, and improve product quality. One of the most promising solutions that have emerged in recent years is the use of collaborative robot arms or cobots. These innovative devices are transforming assembly processes by offering a blend of cost-effectiveness and advanced functionality. This article delves into the advantages of using cobot arms for assembly solutions, exploring their benefits, implementation strategies, and future trends.
Understanding Cobot Arms
Cobot arms, or collaborative robots, are designed to work alongside human operators in a shared workspace. Unlike traditional industrial robots that are often caged off for safety reasons, cobots are built with sensors and advanced safety features that allow them to operate safely near people. This collaboration enables them to assistpeople with various tasks, making them highly versatile and adaptable to different production environments.
The evolution of cobot arms represents a significant shift from the larger, more complex industrial robots of the past. Initially, industrial robots were large, expensive, and primarily used in high-volume manufacturing settings. They required extensive programming and maintenance, which often made them impractical for smaller businesses. Cobot arms, in contrast, are designed to be more user-friendly and cost-effective, providing a valuable solution for a wider range of applications.
Cobot arms are often referred to as “assembly robots” due to their role in automating various tasks within assembly processes. They can be employed to perform repetitive or precision tasks that would otherwise require manual labor. This role highlights their ability to streamline production and enhance efficiency, making them a key component in modern assembly lines.
The Cost-Effectiveness of Cobot Arms
One of the primary advantages of cobot arms is their cost-effectiveness. When compared to traditional robotic systems, cobots offer a lower initial investment. This is due to their simpler design, reduced need for extensive programming, and the fact that they do not require large safety enclosures. This makes them an attractive option for companies looking to automate processes without incurring prohibitive costs.
In addition to their lower upfront costs, cobots can lead to significant long-term savings. They enhance operational efficiency by reducing cycle times and increasing production rates. The ability to quickly reprogram and reconfigure cobots means that they can adapt to different tasks and production requirements with minimal downtime. This flexibility contributes to a more efficient production process and helps businesses respond more rapidly to changing market demands.
Labor cost reduction is another significant benefit of using cobot arms. These robots can perform repetitive and precision tasks that would otherwise require skilled human labor. By taking over such tasks, cobots reduce the need for highly specialized workers, which can lower overall labor costs. Additionally, the training time required for operators to work with cobots is generally shorter than that for traditional robots, further contributing to cost savings.
Advantages of Cobot Arms in Assembly
The flexibility and adaptability of cobot arms are among their most compelling features. These robots can be easily reprogrammed and reconfigured to handle various tasks, which makes them suitable for diverse applications. Whether it is assembling small electronic components or handling heavier parts, cobots can be tailored to meet the specific needs of a production line. This adaptability not only maximizes their utility but also allows businesses to adjust quickly to new products or changes in production volume.
Safety is a critical concern in manufacturing environments, and cobots address this issue effectively. Equipped with advanced sensors and safety features, cobots are designed to operate safely alongside human workers. They can detect the presence of nearby individuals and adjust their movements to avoid accidents, which minimizes the risk of injury. This collaborative approach to automation enhances overall workplace safety and can contribute to a more positive working environment.
Implementing Cobot Arms: Best Practices
When considering the implementation of cobot arms, it is important to start by evaluating your current assembly processes. Assessing the existing workflows and identifying tasks that are repetitive or require high precision can help determine where cobots can be most effectively utilized. This evaluation should include a thorough analysis of the tasks that would benefit from automation and the potential impact on overall production efficiency.
Choosing the right cobot arm involves several considerations. Factors such as payload capacity, reach, and precision should be evaluated to ensure that the chosen model meets the specific needs of your assembly operations. Comparing different models and manufacturers can help identify the best fit for your requirements. Additionally, it is important to consider the ease of integration with existing equipment and software systems to ensure a smooth implementation process.
Conclusion
Cobot arms represent a powerful and cost-effective solution for modern assembly processes. Their ability to enhance efficiency, reduce costs, and improve product quality makes them an attractive option for a wide range of manufacturing applications. By understanding the benefits of cobot technology, implementing best practices, and staying informed about future trends, businesses can leverage the advantages of cobots to optimize their assembly operations and achieve greater success in an increasingly competitive market.