Four tips for faster 3D printing
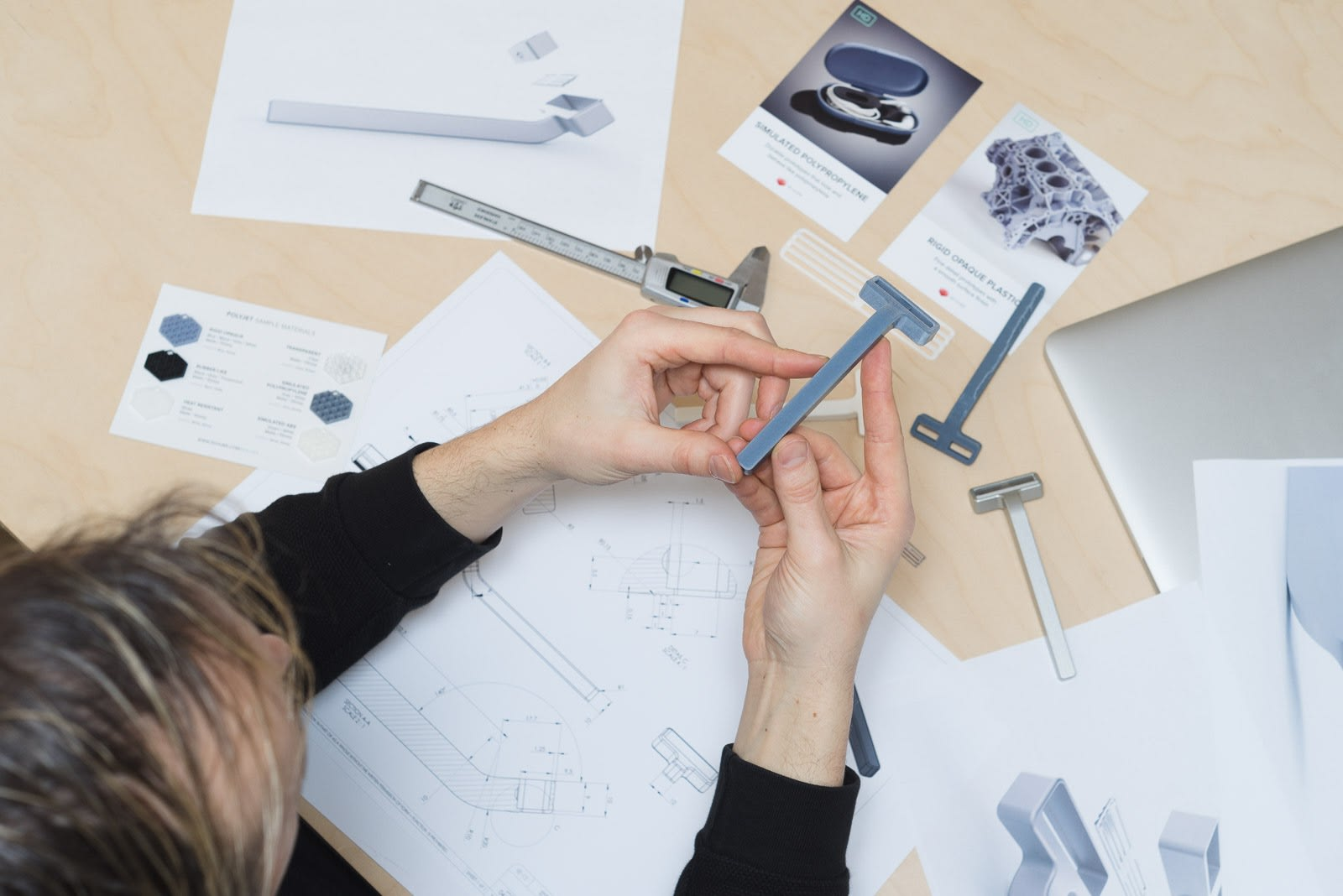
In some instances, 3D printing simply cannot go fast enough. After all, you want to have your product or prototype ready as soon as possible. By employing a 3D printing service, you know this will be the case. However, if you do the 3D printing in-house this depends on your own abilities and qualities. Thankfully speed and quality work like two communicating vessels with additive manufacturing. Faster 3d printing online is possible, but usually it unfortunately has direct consequences for the print quality. This is also the case when it comes to CNC services usually. Below four tips are mentioned that will enable you to get your 3D printed product faster in your hands.
Larger nozzle and layer height
The more filament is pressed through the nozzle during the additive manufacturing process, the faster your 3D print will be ready. With a larger nozzle diameter and higher layer height, you can therefore save a lot of time. But it has a big downside too as thicker print layers unfortunately come at the expense of detail. In addition, the firmness may decrease when you decide to make the nozzle and layer height larger. A larger nozzle and a different layer height therefore only make sense if accuracy is less important, which is not always the case. However, when 3D printing a prototype it could be a good idea to employ this tip.
Increase default speed
FDM printers can achieve high print speeds. However, the problems then arise in the corners and in the fine details. This is the case since the print head must quickly change direction during printing when it should be done in a quick manner. Of course, this is reflected in the quality of the created print. In the places where the print head had to change direction quickly, the quality will be worse. You should therefore take a good look at your model before you decide to increase the print speed, which is possible in the slicer software. A higher speed is usually not a problem for rectangular products, but if fine details have to be 3D printed or if the model has many corners, increasing the default speed is not advised.
Support material
What you can really save printing time with is the choice of support materials if you have a 3D printer with a double extruder. Even though water-soluble filament for the support structures is useful, it does take extra time when printing. And although the support is solved automatically as soon as the workpiece is in water, it does take time. Do you need your workpiece faster? In this case you should check the option in the slicer software to print support from the same material as the one you will use for the workpiece. The 3D printer then prints the support in a lighter pattern so that you can easily break down the structures by hand.
Infill structure and outer layers
The amount of infill can also be employed to save time in most cases. It will almost never be necessary to print a solid piece. The honeycomb structure in the product provides strength, saves filament and shortens the printing time. It is possible to select a certain percentage of infill in the slicer software. The lower this is, the faster the 3D print is ready. However, you should keep the intended application of the print in mind. After all, the smaller the infill, the weaker the product will be. Also note the number of outer layers. Too many solid outer layers in combination with too little infill can cause the outer layers to sag.