Using CNC For Turning And Milling: Understanding The Differences
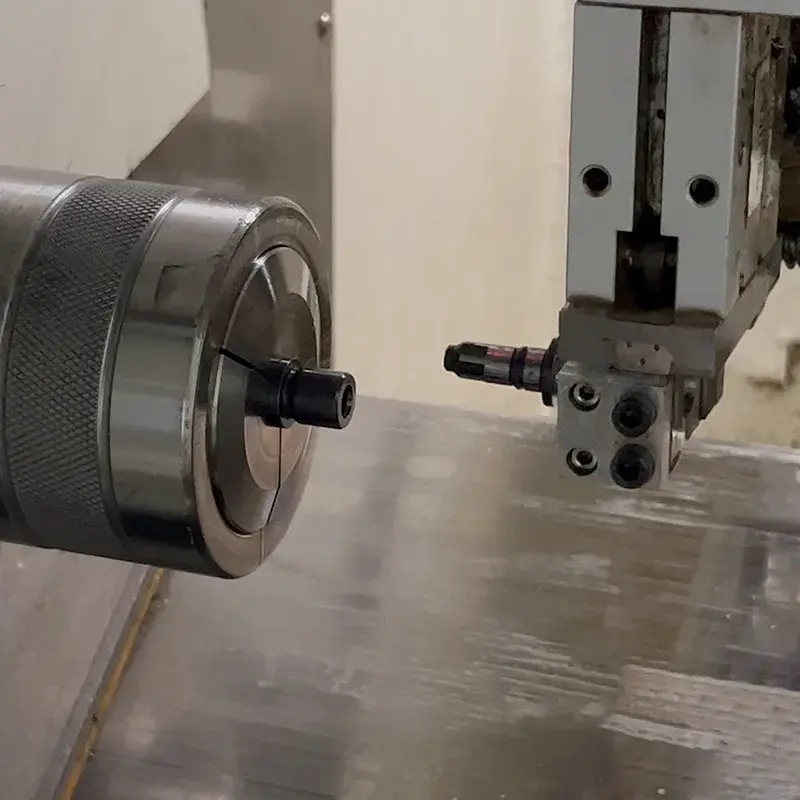
While reading about CNC machining, you might have come across some of the words Turning and Milling. If so, you could need clarification on the meaning of these processes and are looking to learn about the differences.
This article provides fundamentals of the two manufacturing processes, including how they operate and their best applications. Learn more to understand milling and turning and milling, the capabilities each one is proficient at and what process could be the best for your specific project.
What exactly is CNC milling?
When using the CNC milling process, the machine uses the accuracy of computerized control to move and rotate the cutting tools in multi-cutting.
As the raw material progresses through a pre-programmed machine operation, the machine will move across the three main axes for cutting the material. The 5-axis CNC milling machine is a good choice for parts requiring a lot of machining.
With CNC mills, it holds the workpiece in place by securing it on the bed of the machine with the aid of an edging.
Multi-axis CNC milling machine rotates the workpiece, resulting in greater angles for machining. It allows the machinists to create intricate parts. It doesn’t need any manual adjustments to how the piece is positioned.
What is CNC Turning?
The turning process causes a piece of work to rotate as a cutting tool is used to remove the material. This tool is usually one-point, a non-rotating device that is moved along the workpiece and continues to remove layers of material by the plan until it is in line with the design.
Before the introduction of computers to this field, it was a manual process that required continuous supervision to meet the goals set. Today, automated machines usually carry out turning based on algorithms and numerical rules.
With state-of-the-art equipment, cutting-edge technology, and highly skilled personnel, CNC turning services supplier provides a wide range of quality services. They specialize in machining high-precision components with intricate geometries using sophisticated methods such as threading, forming, and drilling.
Utilizing the latest in CAD/CAM software and programming, their team is able to accurately produce a component of any size or complexity, from simple to complex components.
CNC Turning: Methods
Different turning operations are used to cut various shapes for the workpiece.
-
Hard turning
The hard turning process consists of turning the workpiece over the 45-HRC limit. It is an excellent choice as an alternative to the grinding process.
-
Tapered-turning
In taper turning, the canonical surface is formed by the gradual reductions from one area to the next.
-
Drilling
The process of drilling creates a round hole in the workpiece to eliminate the material. The drilling is done by securely securing the drill press used for standard drilling inside the turret on the lathe.
-
Boring
Boring is the method to widen the workpiece’s hole by subtracting material using a single-point cutting tool. Boring is used to create holes with precise dimensions and tapered holes.
Machined parts made by CNC turning
Here is the complete list of components that are made by CNC turning:
Bolts and nuts: The accuracy that CNC turns allow using of items that require tolerances like nuts or bolts.
Turbines: CNC rotating can make circular turbine blades ideal for the energy sector.
Nozzles: They are cylindrical and have hollow interiors, which makes them suitable to be used in the CNC turning process.
Ball joints: CNC turning is the best choice for connecting rounded devices like ball joints.
Rollers: CNC Lathes make rollers and have precision tolerances, which are ideal for industrial applications.
CNC milling techniques
Here are a few of the CNC milling techniques:
-
Form milling
Form milling produces cuts that are not flat, such as curves, contours, and many more. Every kind of curve requires a particular cutting machine to make precise cuts.
-
Plain milling
The name surface milling can also refer to the process of plain milling. In this milling procedure, the cutting tool is utilized to remove the material that is on its surface piece. The rotation axis runs directly parallel to the piece of work.
-
Angular milling
This milling technique uses the cutting tool’s rotary axis at an angle with the workpiece’s surface to make angles as per the plan.
-
Face milling
Face milling employs a rotational axis perpendicular to the material’s surface. It is placed towards the workpiece to take away the material.
Parts made with CNC Milling
Here’s the listing of components that can be made by CNC milling:
Punches for forming: CNC mills create other manufacturing equipment for forming forces to fabricate sheet metal.
Gears: The CNC process is used to produce straight and spiral gears used in mechanical equipment.
Housings and enclosures: The electrical devices and other items can be fitted with custom-milled enclosures that ensure the safety of internal components.
Mould milling: Tooling made from steel permits rapid prototyping of the moulded components.
Medical devices: CNC mills for medical devices are ideal for manufacturing implant devices, surgical tools, and other medical devices.
How Do Milling and Turning Differ?
The primary distinction between CNC milling and CNC turning is in the motion of the cutting instrument and workpiece. In CNC turning, the workpiece is rotated or turned at a predetermined pace while the cutting process remains stationary. The reverse is also true. CNC milling is the process of keeping the workpiece fixed while the cutting tool rotates around it to remove the excess material.
Simply put, the difference in the cutting tool’s movement or workpiece’s motion reflects variations in the dimensions and shapes that each machining method could most efficiently create. Here are some more notable distinctions between milling and CNC turning:
-
Machining Operations
CNC milling is a machining process that includes plain, angular or face milling techniques. In comparison, CNC turning encompasses machining procedures like grooving, drilling, boring, straight, threading, and knurling.
-
Compatible Materials
CNC turning is highly versatile to various materials, such as metals, plastics and wood. However, CNC milling has more specific material compatibility. So, experts generally employ CNC milling to process materials like aluminium, carbon steel, stainless steel, titanium and nylon.
-
Tool Features
CNC turning employs the single-point cutting tool, while CNC milling processes use Multi-point Cutting tools.
-
Shapes Produced
CNC turning is ideal for producing components that have an axially symmetrical shape. These include disks, cylinder cones, polygons, and cones. Additionally, CNC milling can produce parts with both non-symmetrical and symmetrical shapes.