3D Printed Car Parts: How Additive Manufacturing is Changing Automotive Industry
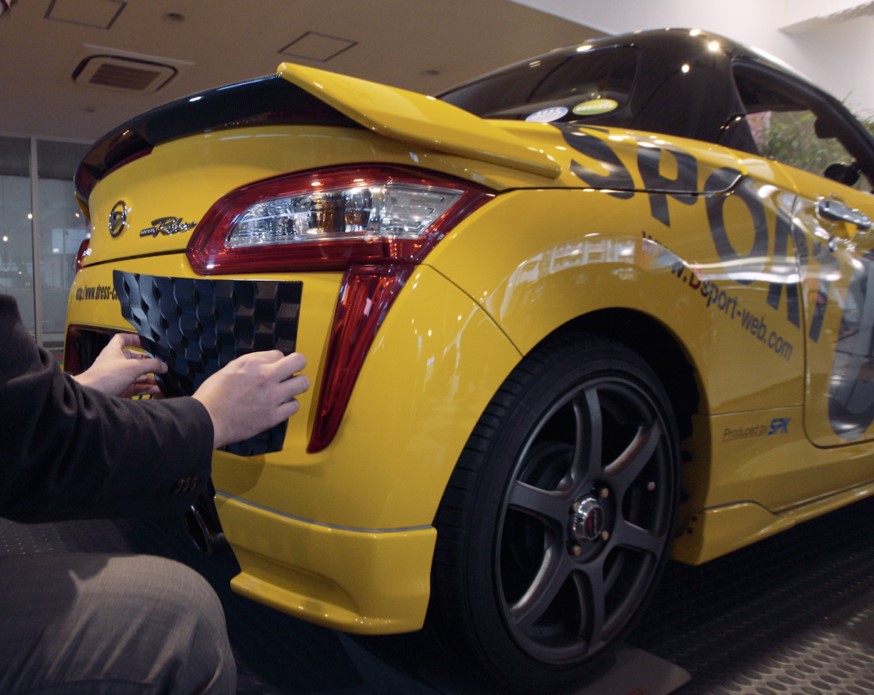
3d printing is changing the entire industrial domain with its innovative advancements. Among all, the automotive field is way ahead when it comes to leveraging the full benefits of additive manufacturing. Be it designing, prototyping, personalization, or batch production, this technology acts as a catalyst for automakers.
For a decade, the main application of additive manufacturing was only finite to essential prototyping and demonstration of ideas. However, companies are using advanced 3d printing technologies like fused filament fabrication (FFF) to build robust and high-performance parts. With growing demands, several companies are now offering 3d printing service in Perth, Melbourne and many other cities. Additive manufacturing is here to stay and grow with us in 2021 and beyond. By 2023, the market valuation of 3d printed parts in the automotive industry will touch the mark of $2,730 Million.
Transforming Impact Of 3D Printing Technology on The Automotive Sector
With ever-growing customer demands and the need for shear innovations, automakers are using additive manufacturing for various applications. When this technology was relatively new, manufacturers only used to create static prototypes to showcase the ideology behind the innovation.
However, as the technology progressed, carmakers started using it to create functional prototypes and small spare parts for real cars. For making the vehicles lightweight and performance-driven, engineers are now using 3d printed components made up of titanium, aluminium and carbon fibre.
Additive technology’s impact in the automotive industry is massive as more companies are now using 3d printed parts in their vehicles. There are several reasons why these 3d printed custom parts are gaining so much popularity among customers. Some of the critical benefits of 3d printed parts are:
Lightweight Parts
3d printing solutions let car manufacturers produce lightweight yet more robust custom parts that enhance a vehicle’s performance. Using metal 3d printing technology, it has become easier for engineers to craft complex machine geometries faster than traditional methods.
Using materials like aluminium, carbon fibre, and stainless steel, automotive manufacturers can create parts with a greater lifespan and cost less to produce. The ultimate benefit of lightweight components is a seamless performance of the vehicle along with less fuel consumption.
Lower Material Wastage
3d printing is an additive method in which the production happens in a layer-by-layer fashion. With this approach, the material wastage is very minimum, and hence it helps in cost optimization. Preparing automotive prototypes and functional parts using 3d printing is more sustainable as compared to conventional manufacturing.
Engineers can produce more complex parts in fewer materials with 3d printing, and that’s why many automakers are gradually diversifying towards this technique.
Higher Personalization
Before additive manufacturing, the scope of modifying a single automotive part was finite, and the process was time-consuming and expensive. However, now it is possible to create a fully custom component regardless of batch size. Engineers can now produce a 3d printing prototype or a batch of products in a faster turnaround time. From custom-made engine parts to modified accessories — now customers can pick how they want their car to look.
Easier Parts Replacement
Earlier, replacing a functional part of a vehicle was way higher and used to take substantial time. But now, companies have their own in-house 3d printing team that produce spare parts in as minimum as a couple of hours. It has become seamless to replace any part of the vehicles at lower costs.
With 3d printing rapid prototyping, manufacturers can design, validate, produce and test a replacement part at a fraction of traditional manufacturing cost.
Cost Optimization
Cost optimization is among the most significant factors behind the rapid growth and popularity of this technology. As compared to conventional manufacturing, 3d printing is cost-efficient and can replace certain traditional operations. Industrial operations like rapid prototyping, small-batch production, or custom parts manufacturing are more affordable to perform with AM. However, there are many core automotive applications where traditional processes are suitable, like mass manufacturing.
Types of Car Parts Built Using 3D Printing
The potential for building custom parts for vehicles is endless, and there are hundreds of small and big parts that companies are manufacturing. Some of the key 3d printed car parts are:
- Custom unibody chassis for sports car
- Personalized gear knobs and dashboards
- Fully-functional large-size car engine
- 3d-printed brake callipers
- Smaller spare parts like brake pads & personalized tyre rims
Among these, manufacturers are creating various car parts using 3d printing technology that is improving overall performance and aesthetics.
Additive Manufacturing Future in The Automotive Industry
3d printing technology is improving how companies are innovating and manufacturing their vehicles and custom parts. In the upcoming time, more companies and small OEMs will adopt this technology to deliver high-quality products.
Currently, many companies are offering professional 3d printing in Australia and other countries to empower automotive and other sectors. As the availability of additive manufacturing increases, we will see more mainstream implementations of this advancement.